Water treatment processes
1 Drinking water
Drinking water is a natural product and its quality is regulated by law in the Drinking Water Ordinance. In practice, a wide variety of areas for e.g. the use of drinking water, its treatment, monitoring, quality testing, protection, … are dealt with in depth by a wide variety of guidelines, legal principles, recommendations and regulations.
High demands must be placed on the quality of drinking water. Since pathogens, if they were to enter the drinking water network, could reach and infect people, this risk must be kept very low. Substances that enter drinking water would, if necessary, expose us to them on a daily basis for the rest of our lives. Therefore, it is important to keep “foreign substances” out of drinking water.
Barriers against contamination are important in the entire process chain, namely during winning, treatment and distribution of drinking water: If the resource is well protected, less technical treatment is required. If distribution systems are built, maintained, and operated according to the technical rules, no contamination will occur in them due to the release of substances from the materials or due to the growth of, for example, legionella or other microbiological pathogens. Decisive for the drinking water qualityis therefore the management of the systems. This is the responsibility of the operators, i.e. water suppliers and owners or operators of buildings. Government monitoring is carried out by the health offices under the responsibility of the states and municipalities.
In Hildesheim, Lower Saxony, the water quality is very good. The city is supplied with water by the Harzwasserwerke on behalf of EVI Hildesheim. This comes from the waterworks Söse I. In this waterworks, surface water from the Granetal Reservoir and the Söse Reservoir is extracted and treated. Regular controls guarantee the constantly high quality and the adherence to all values of the drinking water regulation. With values of approx. 3 °dH, the drinking water in Hildesheim and the surrounding area is very soft. This is pleasant to use, but also means that the water contains relatively few minerals.
2 Why treat water?
Although drinking water is one of the most controlled foods in our latitudes, water quality varies greatly from place to place. Moreover, it is important to distinguish between actually detected and subjectively perceived drinking water quality. Even without detectable pollutants, water quality can be impaired by unpleasant tastes, odors, discoloration or too high water hardness.
Through the targeted use of water treatment processes, almost any “source water” can be treated for a specific application or purpose. Softening, for example, produces so-called “soft water”. This prevents, among other things, any limescale deposits in the water-bearing systems.
Dissolved minerals such as barium, lead, chromium, sodium, fluorine, nitrate, selenium, zinc, copper or rust from the water pipe system can also be reliably eliminated with further water treatment processes such as membrane and filter processes. This prevents damage to the domestic installation and technical equipment from the outset and saves energy at the same time.
Furthermore, an important task of industrial water treatment is to ensure that water can be produced on site from natural resources, such as well water, groundwater or surface water, which meets the legal requirements or the requirements of special consumers, such as cooling towers, beverage manufacturers, clinics, the automotive industry or laundries.
Modern water treatment technology makes it possible to produce the desired water quality by combining the available processes for almost any application.
The technology and mode of action of the legally approved products and processes established on the market vary.
The most important are:
Solid substances in the water, such as sand grains or rust particles, not only contaminate the drinking water, they can also cause long-term damage to the domestic installation, resulting in corrosion or pitting, clogging fittings and contaminating household appliances. Fine and backwash filters provide a comparatively simple, effective remedy by mechanically filtering out all solid particles from the water.
Modern heating systems are becoming more and more technically complex and have sensitive components. In order to function properly, they place specific requirements on the filling water. Only fully demineralized water, so-called VE water, avoids corrosion and disturbing deposits and ensures a consistently high efficiency.
Hard water causes unsightly deposits and leads to scaling of pipes and household appliances. In addition, energy consumption increases with increasing calcification. In the so-called “ion exchange process”, hardness constituents such as calcium and magnesium are replaced by sodium. This process is known as softening and is nowadays used not only in industry but also in the home. In a partial flow process, the softened water is mixed with the original water and thus “blended” to the desired low water hardness.
In industrial applications, the qualitative monitoring of water hardness by means of online measurement technology has become established. Depending on the measurement requirements, so-called limit value measuring devices or actual value analyzers are used for this purpose. Gebrüder Heyl has been a leader in this field for more than 60 years and serves its customers with a portfolio of more than 15 measuring instruments for the determination of water hardness. These include, for example, instruments for measuring alkalinity, with integrated calibration function, certifications for 72-hour BOB operation and UL certification (Testomat EVO TH) or combination instruments such as the Testomat 2000 THCL for measuring total chlorine and residual water hardness.
3 Design and operation of a water treatment plant
There is a big difference between the limits of drinking water and those of process-permitted limits.
In addition, the chemical composition (proportion of dissolved substances in the water) is always different. It is therefore imperative that the water treatment be adapted to the starting material “drinking water” in order to comply with the necessary limit values.
The primary process steps that lead from drinking water to industrially usable water are:
- filtration (sediment filter, activated carbon)
- Softening plant
- Membrane filtration process (nanofiltration, reverse osmosis, …)
- Electrodeionization
- Mixed bed
- Disinfection (UV, ozone, chemical disinfection, thermal disinfection) and
- distillation
Salts are a component in all natural water. Depending on the origin of the water and the type of extraction, the type and concentration of water constituents in drinking water vary.
3.1 Filtration via activated carbon
Filtration via activated carbon is not usually used for solids and particle separation in the context of water treatment. Depending on the type and nature of the suspended solids, so-called sediment filters are used for this purpose. The main use of activated carbons is the adsorption of organic and inorganic water constituents. In some cases, this process is also used to protect membrane systems, such as reverse osmosis, from products containing chlorine, as these damage the membranes.
During production, coals based on hard coal or coconut are thermally activated. This produces the very large inner surface typical of activated carbons. The inner surfaces adsorb many chemical trace substances until they reach equilibrium. This equilibrium zone shifts in the direction of filtration during operation, i.e. the filter loads up to breakthrough. For this reason, activated carbon filters must not be flushed in adsorption applications. Loaded or exhausted material must be replaced with virgin or regenerated material. Activated carbon also acts as a reducing agent for ozone and chlorine, but this results in material depletion.
Filtration via activated carbon is primarily used to remove
- excess chlorine
- Odor
- Color
- taste and
- halogenated hydrocarbons
used.
3.2 Softening plant
3.2.1 How a water softener works
There are two main processes for water softening. These are the ion exchange process and physical water softening. The phyiskalische water softening could not become generally accepted however due to the hardly or not existing effect mode, so that the ion exchange procedure became generally accepted as the standard with the water softening.
Ion exchange process
The most commonly used water softening process is the ion exchange process. Here, the water to be softened flows through a container filled with cation exchange resin, which is also referred to as a column. Inside the container, the calcium and magnesium ions contained in the water are replaced by the sodium ions bound in the cation exchange resin. The water loses the hardness-forming calcium and magnesium ions and thus becomes “soft” (softened). This process works until the cation exchange resin has released all its Na+ ions. Therefore, the cation exchange resin must be regenerated regularly. For this purpose, the exchanger resin is rinsed with a diluted sodium chloride solution (salt solution). During rinsing, the cation exchange resin releases the bound calcium and magnesium ions and replaces them with fresh Na+ ions. The process of flushing is also called regeneration of the water softener. During the regeneration process, the cation exchange resin cannot soften water.
If only one column with cation exchange resin is available in the softening plant, no softened water is available for the time of regeneration.
For the above reason, a so-called double softening system is generally used in the industrial environment. This consists of at least two columns. If one column is in regeneration, the other column continues to produce soft water. This ensures a continuous supply of soft water to the consumers.
Im Vergleich zur zeit- oder mengenbezogenen Regenerationsauslösung hat die qualitative Regenerationsauslösung den Vorteil, dass die Kapazität der Enthärtungsanlage vollständig genutzt wird. Hierdurch wird der salzbedarf für die Regeneration sowie das anfallende Abwasser minimiert. Weiterhin ist hierdurch sichergestellt, dass die Regeneration auch bei Abbau der verfügbaren Kapazität durch bspw. Alterung des Harzes oder stark schwankenden Abnahmen zu jederzeit verlässlich arbeitet und somit kein „hartes“ Wasser in die nachgeschalteten Prozesse gelangt.
3.3 Membrane process
There are different ways of water treatment. The untreated well or surface water is called raw water. Both surface and well water often have elevated parameters that can cause problems when this untreated water is used. These parameters provide insight into water quality. The desired water quality depends on what the business or user needs the water for. The elevated parameters and desired water quality also determine the type of water purification system.
The most common water treatment plants are:
- Open preparation
- Closed preparation
- Osmosis filtration
- Nanofiltration
- Ion exchanger
- UV filtration
- Dosing devices
When purchasing a particular water treatment system, it is also important to consider the ongoing costs.
- Energy consumption per m3 of purified water
- Maintenance costs
- Additives for water purification
Reverse osmosis
The reverse osmosis process belongs to the so-called closed treatment systems. A closed treatment means that the purification takes place without direct contact with the oxygen. However, in some types of treatment, oxygen is used in the water treatment process. However, it is added in a controlled manner, for example, by a compressor. Many of the closed treatment systems used utilize membrane technology in the water purification process. Also, ion exchangers are often added to the design of closed treatment systems.
A distinction must be made between:
Process name | Cut-off line | |
Microfiltration | 0,2 µm | 0.2 to 5 bar |
Ultrafiltration | 0,1 µm | 1.0 to 10 bar |
Nanofiltration | 0,01 µm | 5.0 to 10 bar |
Reverse osmosis | 0,001 µm | 10 to 150 bar |
Reverse osmosis or reversosmosis is a physical process for concentrating substances dissolved in liquids, using pressure to reverse the natural osmosis process.
It is used to treat water for drinking and process water, to treat wastewater and to treat aquarium water. Fruit juice concentrates are also produced according to this principle.
The medium in which the concentration of a particular substance is to be reduced is separated by a semipermeable (semipermeable) membrane from the medium in which the concentration is to be increased. This is subjected to a pressure that must be higher than the pressure created by the osmotic demand to balance the concentration (osmotic pressure). This allows the molecules of the solvent to migrate against their “natural” osmotic propagation direction into the area where the solutes are already less concentrated.
Drinking water has an osmotic pressure of less than 2 bar, the applied pressure for reverse osmosis of drinking water is 4 to 30 bar, depending on the membrane and system configuration used. Other liquids have higher osmotic pressures, e.g., seawater about 30 bar depending on salinity. Accordingly, the pressures used for seawater desalination are 60 to 80 bar. In some extreme applications, e.g. for the concentration of landfill leachate, even significantly higher pressures are used for process engineering purposes.
The osmotic membrane, which allows only the carrier liquid (solvent) to pass through and retains the solutes, must be able to withstand this high pressure. When the pressure differential more than compensates for the osmotic gradient, the molecules pass through the membrane while the “contaminant” molecules are retained. Unlike a classical membrane filter, osmotic membranes do not have continuous pores. Rather, ions and molecules migrate through the membrane by diffusing through the membrane material. The solution diffusion model describes this process.
The osmotic pressure increases with increasing concentration difference. If the osmotic pressure becomes equal to the applied pressure, the process comes to a standstill. To counteract this, the concentrate is discharged steadily. Since crystallization (precipitation) of the solutes (salt or minerals) in the membranes must be prevented, the use of reverse osmosis is only useful up to a certain maximum concentration of concentrate flow.
Note: The yield of a reverse osmosis (recovery rate RO) is plant and operating mode-related between 50 – 98%. At the same time, up to 99% of the dissolved water constituents are separated..
Microfiltration and ultrafiltration
Suspended solids, turbidity and microorganisms can be removed excellently with the help of ultrafiltration. Both techniques are therefore often used as pre-treatment for reverse osmosis and are an alternative to more traditional water treatment techniques such as sand filtration.
The difference between microfiltration and ultrafiltration is the diameter of the membrane pores. Microfiltration pores are in the size of 0.1 – 10 µm and are able to retain bacteria completely and viruses partially. Ultrafiltration pores have a diameter of 0.005 – 0.1 µm and can also completely remove viruses from the water.
The main advantages of microfiltration and ultrafiltration are:
- Far-reaching removal of dissolved and colloidal particles compared to traditional techniques
- Compact and modular design of the system, thus small footprint and flexible operational management
Microfiltration and ultrafiltration are physical separation processes that work according to the sieve effect. Separation occurs according to particle size. Particles larger than the membrane pores are stopped by the membrane. The driving force for microfiltration and ultrafiltration is a pressure difference across the membrane between the inlet and filtrate sides. Both membrane types can be operated dead-end or cross-flow. In dead-end operation, all water is forced through the membrane. In cross-flow operation, the introduced raw water is circulated along the membrane surface. Due to the resulting turbulence, heavily fouled water streams can be treated. The membrane surface must be cleaned periodically. Cleaning can be done in several ways. The best known is backwashing the membrane with filtrate. Air flushing along the raw water side of the membrane is also possible. Furthermore, chemical cleaning can be applied.
Nanofiltration
It is an extremely modern membrane filtration. This technology largely coincides with osmosis filtration. However, this technology has the great advantage that the water after treatment is not too clean. As a result, no parameters need to be adjusted so that the treated water can be used afterwards for certain purposes, such as drinking water for human consumption.
3.4 Electrodeionization (EDI)
Electrochemical membrane processes are used for residual desalination of treated water. The cells are regenerated only via an applied voltage. This is done during operation, so no interruption is necessary for regeneration. This type of pure water treatment is also called residual desalination or polisher.
Electrodeionization is usually performed after a Reverse osmosis system used to further purify the permeate (product of reverse osmosis). The ultrapure water produced has very low conductivities and low silica levels. For the use of an electrodeionization system, the removal of carbon dioxide from the input water is mandatory. For this purpose, NaOH (lye) can be dosed upstream of the reverse osmosis system to raise the pH value, or a Membrane degassing be used.
Byelectrodeionization a continuous water treatment for pure water production without chemicals can be guaranteed. Storage of large quantities of acids and alkalis is not necessary, except for small quantities of NaOH for raising the pH before the reverse osmosis system. No chemicals are necessary when using membrane degassing. Electrodeionization is of high quality, compact and space saving and requires minimum maintenance with high operational reliability.
Fields of application of electrodeionization
- Semiconductor industry
- Pharmaceutical industry
- Cosmetic industry
- Boiler feed water generation
- Boiler feed water for turbine operation
- Hospitals
- Laboratories
- Chemical industry
- Ultrapure water production
Note: The recovery rate of electrodeionization (EDI) is between 93 – 95% depending on the plant and operating mode..
3.5 Blended bed
Mixed bed exchangers, also called mixed bed filters, are used in water treatment when demineralized water from drinking or industrial water is mixed with Ion exchange resins is to be produced. The mixed bed filters remove the remaining ionogenic compounds from a water, which still remain in the water after pretreatment with other processes. At the same time, the mixed bed is also often used as a so-called “police filter” to catch any breakthroughs from the upstream treatment stages.
The design of mixed bed filters is largely comparable to that of DC exchangers. However, while the latter contain either only cation or anion exchange resins, mixed bed filters basically use at least 2 types, namely a cation and an anion exchange resin. With these two types of exchange resins, water-dissolved Elektrolyte be completely removed. Since two different ion exchange resins are present in one tank, an additional drainage system must be installed in mixed bed filters that are not regenerated externally, so that a spatially separate Regeneration of the resins can be carried out.
3.6 Disinfection process
Disinfection ensures the elimination or killing of a large part of microorganisms. Not all bacteria are destroyed (not sterilization but inactivation due to damage to the DNA strand). Important procedures are:
Chlorine and chlorine dioxide use
Microfiltration
Ozone application
UV irradiation
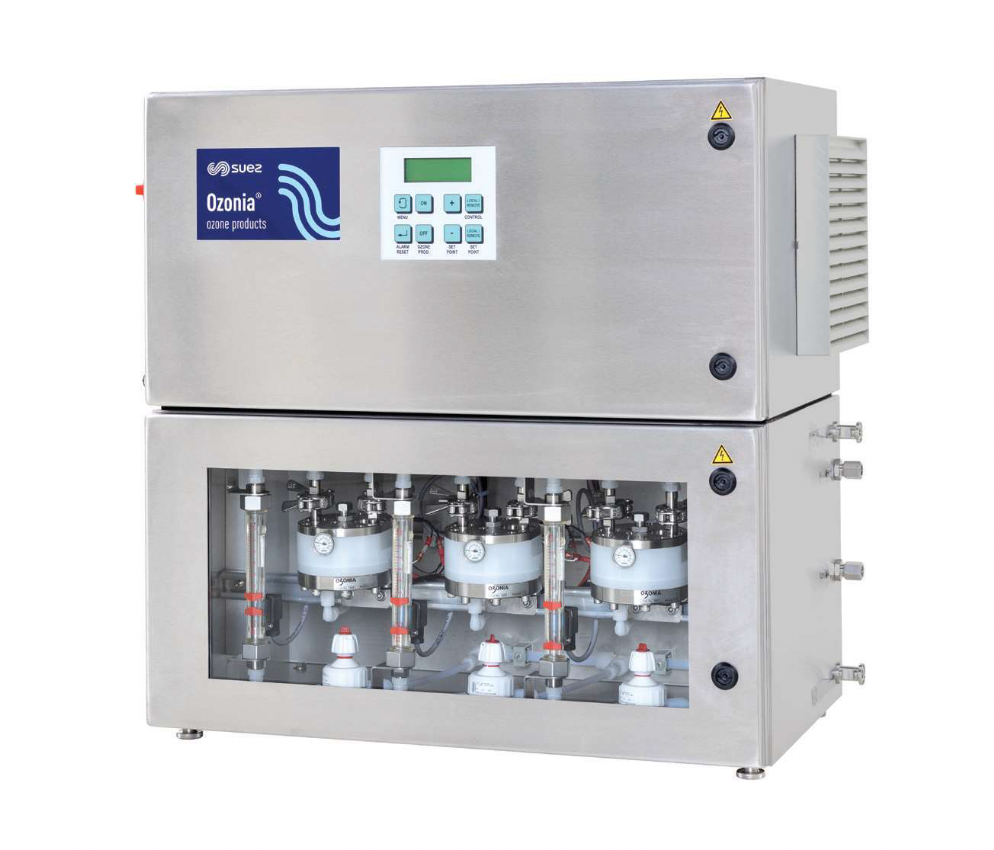
Item no. | Article description |
850941 | Electrolytic ozone generator MkV-S-1, system plant: ozone output 3-4 g/h |
850942 | Electrolytic ozone generator MkV-S-2, system plant: ozone output 2x 3-4 g/h |
850943 | Electrolytic ozone generator MkV-S-3, system plant: ozone output 3x 3-4 g/h |
850951 | Electrolytic ozone generator MkV-K-1, component system: ozone output 3-4 g/h |
850952 | Electrolytic ozone generator MkV-K-2, component plant: ozone output 2x 3-4 g/h |
850953 | Electrolytic ozone generator MkV-K-3, component system: ozone capacity 3x 3-4 g/h |
3.7 Distillation
Distillation retains all ingredients with a higher boiling point than water. This requires a high energy input; moreover, the time required per processed quantity is high.
4 UV disinfection
UV filtration makes use of a UV lamp. The bacteria and organisms in the water are killed by UV light as soon as they pass the UV light. The UV lamp is located in a cylinder, which is installed in the consumption line.
4.1 Dosing devices
These are often needed when the water is already purified, but certain parameters still need to be influenced. Such as the acidity (pH) of the water. They are also often used to combat bacteria, algae and biofilms. With the help of a mixing vessel and a dosing pump, the amount of additives is determined depending on the liter volume and/or torques of a pump. Common additives include: chlorine dioxide, chlorine, caustic soda, citric acid, etc.
The active ingredient can be determined directly by means of photometric online measurement methods to ensure that the product is dosed as required.
Particularly when well water is used, deferrization, demanganization and/or decarbonization is necessary in many cases in order to put the water thus obtained to further use.
Deferrization
Water with elevated iron content (> 0.2 mg/l) must be treated. As a rule, iron-containing waters are reduced or low-oxygen waters in which the iron is usually present dissolved in divalent form as Fe2+. Iron is a heavy metal that is normally present in the earth’s crust only as oxide. During seepage, water, whose oxygen content decreases over time due to biological processes, comes into contact with these oxides in deeper layers of the earth.
When the oxygen content is low, iron oxides are reduced by biological metabolic processes and the iron released in the process is dissolved in water. Although iron dissolved in water is physiologically harmless and not humantoxic, it leads to incrustations and deposits in pipes, fittings (aerators) and machines (e.g. washing machines). Problems can also be caused by microorganisms such as Gallionella (iron eaters). These organisms use the energy released during the oxidation of divalent iron to trivalent iron as an energy source. Under optimal conditions, they form gallery clumps, which can lead to massive problems. For all these reasons, deferrization (and also demanganization), along with filtration, is one of the oldest water treatment processes of all.
Demanganization
Manganese can be almost completely removed from water by demanganization. Manganese often occurs in water at the same time as iron. As a rule, manganese-containing waters are reduced or low-oxygen waters in which the manganese is dissolved in divalent form as Mn2+. Like iron, manganese is a heavy metal that is normally present in the earth’s crust only as an oxide. During seepage, water, whose oxygen content decreases over time due to biological processes, comes into contact with these oxides in deeper layers of the earth. When oxygen levels are low, redox processes occurring in the soil reduce oxides and the manganese released in the process is dissolved in water. Oxidized manganese forms black deposits in pipelines, which can lead to massive problems. Like deferrization, demanganization is one of the oldest water treatment processes of all, along with filtration. In the course of demanganization, the soluble divalent manganese is oxidized with oxygen to insoluble manganese oxide (brownstone). However, pure manganese removal is not as simple as iron removal, since manganese is only oxidized after iron. In classical treatment by aeration, two filter stages are therefore usually connected in series. In the first stage, iron removal takes place and in the second stage, manganese removal.
Decarbonization
Water decarbonization is a very important part of water treatment, necessary to prevent the amount of carbonate hardness responsible for increased precipitation in boiler water. Possible applications for decarbonization are many, including production of boiler feed water, purification of water for use in district heating, or process water in the beverage industry. Frequently, one also speaks of product and partial desalination, which takes place through the exchange of hardness-forming cations.
Decarbonization plants are used in many different industries because groundwater increasingly has high carbonate hardness. Water with excessive hardness is only suitable to a very limited extent for various applications such as use as cooling water or process water.
If the water is also heated during processing, precipitation of calcium carbonate or the formation of the so-called scale occurs very quickly. This can cause damage to plants and also in their piping systems as well as assemblies such as heat exchangers.
Possible applications for decarbonization are as follows:
- the production of boiler feed water, Sustainable water treatment for boiler houses
- the cooling water treatment and steam generation
- the production of district heating water
- the production of process water for breweriesand in areas of the beverage industry
- in the catering industry and for use in automatic dishwashers (for example, in the form of an ion exchanger cartridge)
In order to remove the high carbonate hardness from raw water, various processes are used. For example, water decarbonation can be carried out with special cation exchange resins in weak acid form, whereby the carbonate hardness of a water is exchanged for hydrogen ions. This process produces carbonic acid from the carbonate hardness.
If it is a conventionalsoftening , the hardness-forming cations are exchanged for sodium ions. Complete plants for the production of boiler feed water or other decarbonized water can also handle other parts of the water treatment such as CO2 degassing or even the overall softening of the water.
During decarbonization, water flows through a section of the plant that is filled with a special, weakly acidic cation exchange resin. This results in an exchange of calcium and magnesium ions dissolved in the water for hydrogen ions. The amount of ions exchanged corresponds to the chemically equivalent amount of the concentration of hydrogen carbonate in the water.
In the course of the chemical reactions, the hydrogen ions react with the hydrogen carbonate to form carbonic acid or water with a proportion of carbon dioxide. This can then be removed from the water again if desired, for example by a CO2 trickler.